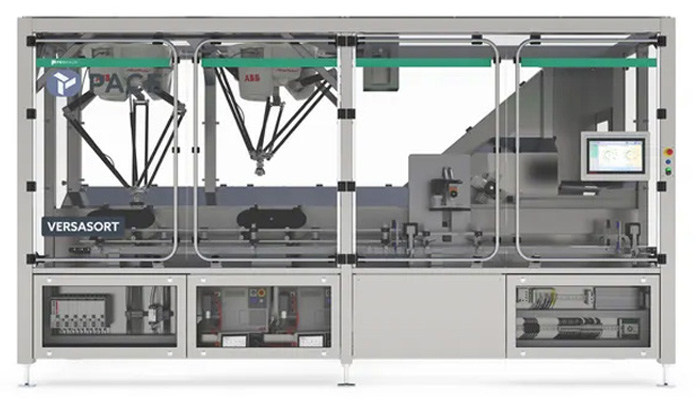
Efficiency is the name of the game in high-speed packaging, and it all starts with bottle orientation. Long before a product is filled, sealed, labeled, or palletized, it has to be reliably unscrambled: aligned upright, single-file, and ready to move seamlessly down the line. Whether you’re producing cold brew in PET bottles, squeezable condiments in HDPE, or glass spirits bottles for seasonal runs, bottle unscrambling is a foundational step.
This early-stage process has a direct impact on throughput, downtime, and quality assurance. As packaging lines become increasingly automated and product SKUs continue to multiply, traditional unscrambling systems often struggle to meet the demands for flexibility, quick changeovers, and gentle handling. Today, forward-thinking manufacturers are taking a look at their unscrambling strategy, and in many cases, modernizing it entirely.
Orientation Challenges Across Market Verticals
Every vertical market has its own packaging challenges, and the bottle unscrambler is where many of them first become apparent.
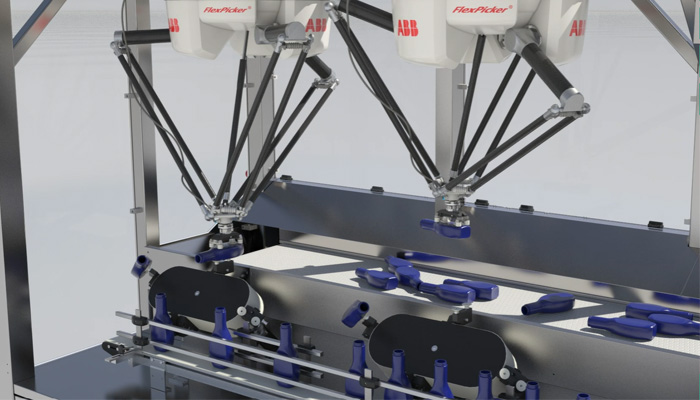
In the Ready-to-Drink (RTD) beverage space, brands are racing to meet demand for functional beverages, energy drinks, and single-serve coffee in uniquely shaped bottles. According to Grand View Research, the RTD category is projected to grow at a rate of over 6% annually through 2030. This growth introduces more variation in packaging—different bottle shapes, heights, neck sizes, and materials—which makes traditional mechanical unscramblers harder to manage without extensive manual intervention.
Liquid foods and condiments pose similar challenges. From curved squeeze bottles to wide-mouth jars, these packages must be carefully handled to prevent tipping, cracking, or misfeeds. And for processors in the dairy sector, where plastic bottles for milk, creamers, and yogurt drinks are lightweight and easily deformed, the unscrambler must balance gentle handling with consistent orientation at high speeds.
Even in the distilled spirits industry, where many operations use pre-oriented glass containers, limited-edition runs, pilot lines, or more generic formats often call for flexible unscrambling technology that won’t slow down production or increase manual labor.
A Smarter System with Pace VersaSort Robotic Unscrambling System
As packaging demands evolve, so does the technology behind bottle orientation. One standout example is the VersaSort™ Robotic Unscrambler from Pace, a ProMach product brand. Featured in Packaging World, VersaSort redefines what a bottle unscrambler can do, especially for manufacturers seeking greater flexibility and performance.
Instead of relying on rotary mechanisms and change parts, VersaSort uses vision-guided delta-style robots to identify and pick bottles from a mass flow, orient them upright, and gently place them into a single-file line. This architecture supports a wide range of container types and sizes with minimal manual changeover, saving time, reducing labor, and increasing consistency. It’s a particularly strong fit for operations handling multiple SKUs or switching between bottle formats frequently.
The Beckhoff Backbone is Precision in Motion
What sets VersaSort apart isn’t just its mechanical flexibility—it’s also the intelligence behind the motion. According to the Packaging World article, VersaSort is powered by a Beckhoff Automation control platform that integrates robotics, machine vision, and servo motion on a single EtherCAT-based network. This enables extremely fast, synchronized communication between all system components, allowing robots to react in real time as bottles enter the field of view.
Rather than relying on separate PLCs and controllers for each subsystem, Beckhoff’s PC-based control consolidates everything into a unified architecture. This significantly simplifies electrical design, reduces programming complexity, and improves response times. For users, that means smoother motion, better uptime, and a platform that can scale as production grows or changes.
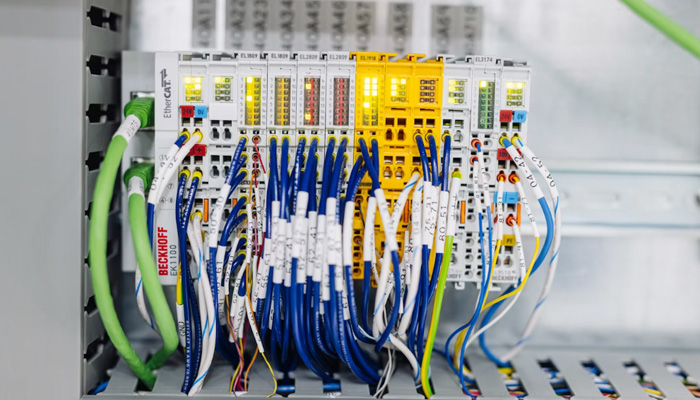
Beckhoff’s system also provides real-time performance data that can feed into overall equipment effectiveness (OEE) tracking, preventative maintenance, or larger digital transformation initiatives. It’s a modern backbone for a modern line—and a great example of how control architecture directly supports packaging performance.
Smarter Bottle Unscrambling for a Flexible Future
While it may not be the flashiest part of the line, bottle unscrambling is where packaging success begins. It sets the pace, literally, for the rest of the operation. As more brands lean into flexible packaging, shorter production runs, and SKU proliferation, outdated mechanical unscramblers may become a limiting factor in overall efficiency.
Solutions like Pace’s VersaSort, backed by automation platforms like Beckhoff’s, are showing that bottle orientation doesn’t have to be the bottleneck. Instead, it can become a smart, scalable, and high-performing piece of the modern packaging puzzle.
For processors and packagers in fast-changing markets like RTD, dairy, condiments, and spirits, that kind of adaptability is essential.
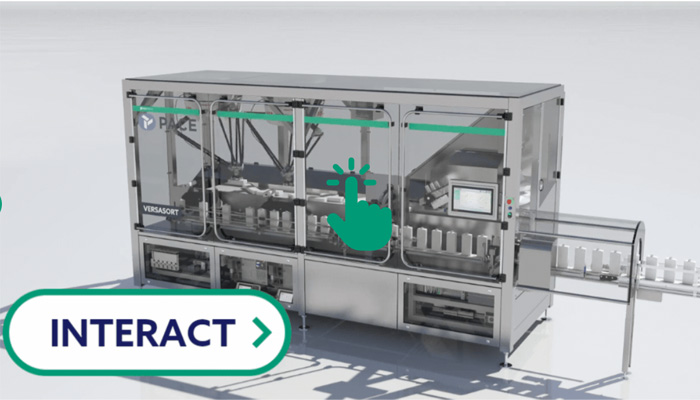
Sources: