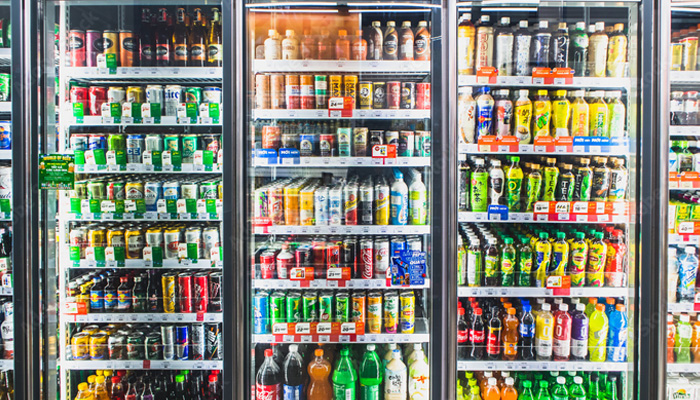
As the global ready-to-drink (RTD) market continues to grow, beverage manufacturers are under increasing pressure to scale operations while maintaining product integrity and line efficiency. Whether it’s cold brew in cans, sparkling teas in bottles, or functional beverages in cartons, RTD packaging requires speed, adaptability, and seamless system coordination.
So what sets a high-performance RTD packaging line apart?
RTD Growth Is Driving Packaging Demands
The surge in RTD consumption, spanning everything from protein waters and adaptogen teas to hard kombucha and canned espresso, has created significant ripple effects across the packaging industry. According to market forecasts, the global RTD segment is expected to exceed $282 billion by 2034, fueled by consumer preferences for convenience, portability, and health-forward formulations.
With this kind of growth comes complexity. Beverage brands are racing to innovate with new ingredients, package formats, and functional claims, all while maintaining safety and shelf life. As a result, packaging lines must be more versatile than ever and able to switch between product types and container sizes without compromising throughput or quality.
Fast, Accurate Filling at the Core
Every high-performance line starts with the filler. Speed and precision must go hand in hand—especially for beverages with low tolerances for overfill, carbonation, or contamination.
Rotary filling systems are purpose-built for beverage lines and can handle hundreds of bottles or cans per minute. For carbonated beverages, counter-pressure filling maintains product integrity and reduces foaming. For still beverages, CIP-compatible designs ensure clean operation between runs, especially important for dairy-based or plant-based SKUs.
Pairing a high-speed filler with Zalkin rotary cappers and P.E. Labellers’ advanced labeling systems ensures that the front half of the line keeps up without creating bottlenecks.
Back-End Integration That Keeps Pace
A line is only as fast as its slowest point, and secondary packaging is often the culprit. To support high-speed primary packaging, modern RTD lines must automate case packing and palletizing just as aggressively.
Robotic and servo-driven systems enable high-speed packing of bottles and cans into a wide range of case formats. These systems are often equipped with vision-guided robotics, multi-SKU handling, and rapid changeover capabilities.
Accumulation systems between machines serve as pressure relief valves, buffering product flow and allowing each part of the line to operate at optimal speed, even during minor disruptions.
Evolving Expectations for Line Performance
High performance is no longer just about maximizing output. It’s also about operational resilience. With labor shortages, tighter margins, and increasing pressure to reduce energy consumption, today’s beverage producers are rethinking what efficiency really means.
Many are shifting toward digitalized operations, leveraging data not just for machine-level diagnostics but for macro-level insights—like predicting downtime before it happens, analyzing product flow trends, and improving sustainability KPIs.
Further, the focus on total line effectiveness is growing. Instead of optimizing equipment in isolation, more manufacturers are designing packaging lines as end-to-end systems. This shift reflects a broader move toward systems thinking—evaluating how each piece of equipment impacts not only line speed but labor needs, maintenance schedules, and product quality over time.
Built-in Flexibility for SKU Proliferation
Today’s RTD landscape is all about variety. One line may need to run different bottle sizes, label types, or product flavors in a single shift. High-performance lines are engineered to adapt without losing efficiency.
Quick-change tooling, servo-driven changeovers, and recipe-based automation allow for faster transitions between SKUs. Labeling and sleeving systems with flexible container handling help producers meet changing demands without sacrificing speed or accuracy.
At scale, it’s this balance between speed and flexibility that determines long-term throughput.
Centralized Control and Smarter Line Insights
Integrated controls are non-negotiable in high-performance environments. RTD packaging lines need a centralized system to monitor throughput, coordinate machine communication, and flag inefficiencies in real time.
Plant managers and line operators alike are looking to line intelligence platforms that provide actionable insights. The ability to drill down into root-cause stoppages, track recipe-level efficiency, and visualize equipment utilization is now considered a baseline for modern operations.
Reliability That Scales
In high-performance lines, uptime is currency. The best equipment isn’t just fast, it’s durable, serviceable, and designed for long-term reliability.
This becomes even more critical in co-packing or multi-client environments, where packaging lines may be required to run around the clock with minimal margin for error. In these cases, component reliability, easy service access, and proven machine-to-machine communication are what keep operations running at peak performance.
The Takeaway
High-performance RTD packaging lines aren’t assembled—they’re engineered. From the moment product enters the filler to the second it’s palletized for shipping, every machine, control system, and operator touchpoint must function in harmony.