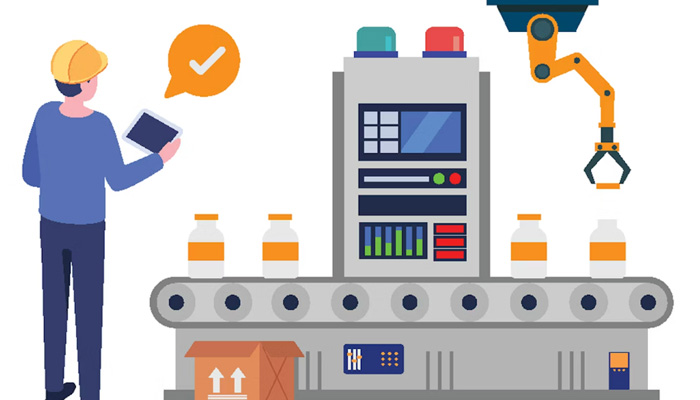
In a recent article from Packaging World, Casey Flanagan discusses the trend of companies leaning on digitalized production lines, the importance of predictive maintenance, and how more and more, packaging and processing companies are using these tools to reduce downtown and cut maintenance costs. From PMMI Business Intelligence’s 2023 report, “Sustainability and Technology – The Future of Packaging and Processing” and 71% of respondents reported said they had some form of predictive maintenance technology in place, compared with just 37% for collaborative robots, the next most popular digitalization initiative.
The benefits mentioned include reducing unplanned downtime, improving productivity, lowering maintenance costs, decreasing MRO inventory, increasing run times, improving overall equipment effectiveness (OEE), and enhancing customer service.
Common Types of Predictive Maintenance
The survey also identified common types of predictive maintenance being employed, such as cloud-based vibration monitoring, AI-based data analytics, and online tracking. The positive impact of predictive maintenance on operational efficiency and cost savings is utilized in a variety of industries, from consumer product goods manufacturers, to e-commerce, and beyond.
This is a topic that ProMach product brand ZPI knows well. ZPI is a leader in developing, implementing, and supporting information-based systems focused on improving the operation, productivity, and Overall Equipment Effectiveness (OEE) of packaging lines and the equipment in them. This topic aligns with ZPI’s focus on providing these solutions with industry trends.
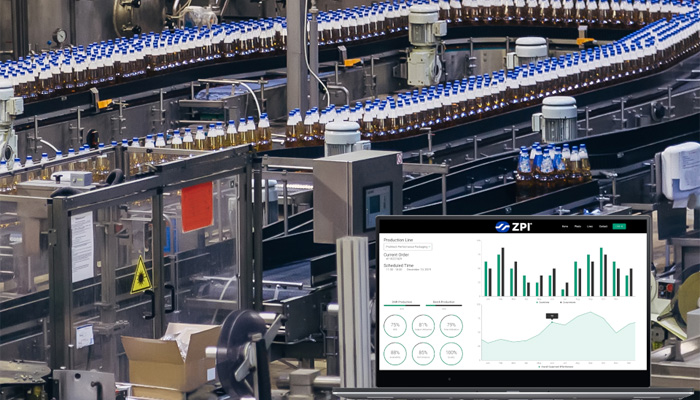
ZPI solution sets include the following:
Monitor and Report: ZPI Monitor & Report is a software-based tool that world-class packaged goods manufacturers use to analyze and maximize the productivity of their packaging lines.
Serialize and Track: Serialize & Track assigns unique identifiers to consumer-facing products and then provides the capability to locate and validate specific units of production anywhere in the distribution channel. Serialize & Track is 100% hardware independent and it can be integrated into existing or new packaging lines. It is compatible with a very wide range of both new and existing equipment types, brands, and models. When operational in a production line Serialize & Track drives the serialized identification of every container, bundle, multi-pack, case, and pallet produced on a production line.
Maintain and Predict: These software systems are designed to deliver real-time condition monitoring (CBM) as well as maintain data analysis, schedule tasks, track critical machine conditions, and more. The maintenance software ensures efficiency and precision for maintaining machine function.
As digitalization efforts increase across production and processing manufacturers, so too will the benefits of predictive maintenance. ProMach product brand ZPI aligns with this growth and their focus is on providing cutting-edge software solutions that align with industry trends.
Read the case study below from ZPI on how a global beverage manufacturer boosts production with help from ZPI. Learn more about ZPI’s solution sets here.